Discovering the Benefits of Sublimation Printing for High-Quality Fabrics
The Surge of DTF Printing: Exploring Its Applications and advantages
The appearance of Straight to Film (DTF) printing modern technology is reinventing the custom clothing sector, providing noteworthy benefits and a large array of applications. As the cravings for custom-made goods continues to broaden, comprehending just how DTF printing can satisfy these advancing needs is progressively crucial.
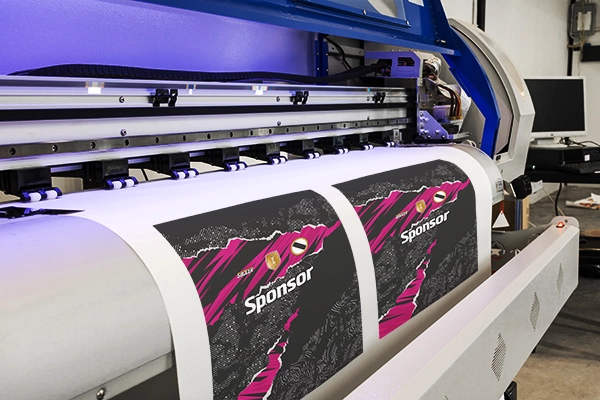
Understanding DTF Printing Technology
Recognizing DTF Printing Innovation marks a considerable improvement in the fabric printing industry, especially for its versatility and effectiveness. Direct-to-Film (DTF) printing is a cutting-edge procedure that includes printing designs onto special transfer films, which are after that moved onto material using heat and pressure. Unlike standard techniques, DTF printing does not require pre-treatment of the textile, allowing a much more streamlined process.
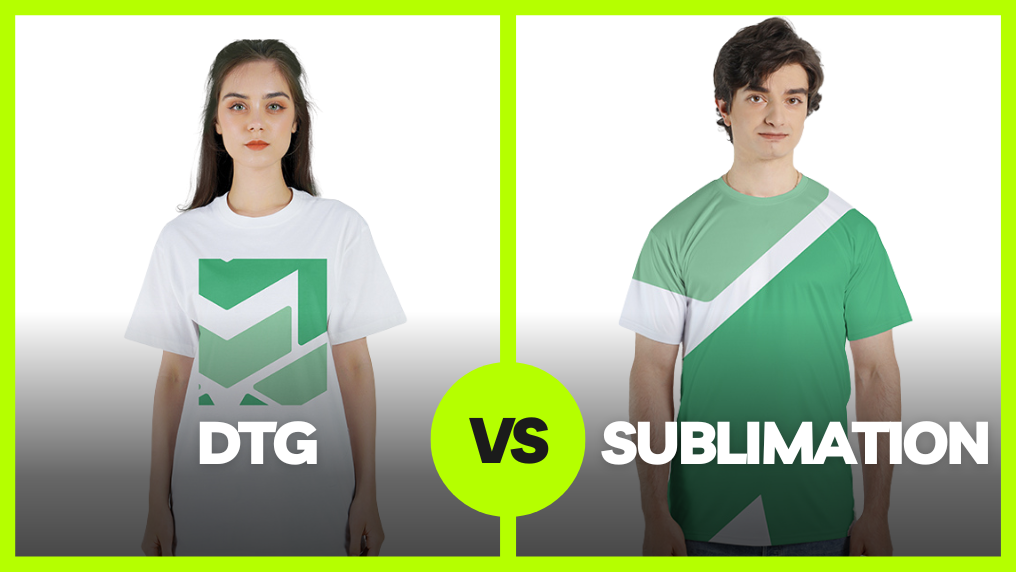
Once healed, the film is placed onto the fabric, and a warm press transfers the design by applying consistent warmth and stress. This leads to dynamic, top quality prints that adhere seamlessly to numerous fabric kinds, including cotton, polyester, and blends (sublimation printing). The technology's capability to generate intricate and brilliant layouts with very little configuration makes it a game-changer in the fabric printing field
Trick Benefits of DTF Printing
Among the vital advantages of DTF printing is its extraordinary flexibility, which enables top notch prints on a broad variety of textile types. This capability expands past conventional cotton to consist of polyester, nylon, natural leather, and even combined materials, making it suitable for varied textile applications. This versatility reduces the requirement for several printing technologies, improving manufacturing procedures and minimizing total costs.
One more substantial advantage is the premium print quality that DTF innovation delivers. By using dynamic, sturdy inks and accurate application approaches, DTF prints keep their shade fidelity and sharpness also after numerous cleans. This results in a product that not just looks specialist but likewise stands the examination of time, giving consistent value to both makers and end-users.
Furthermore, DTF printing uses a streamlined operations, which can lead to enhanced effectiveness and efficiency. Unlike traditional methods such as display printing, DTF does not need intricate arrangement or considerable drying out times. This ease of use makes it an attractive option for businesses of all sizes, enabling quicker turnaround times and the ability to handle small to huge manufacturing keeps up marginal inconvenience.
Applications in Customized Clothing
In the realm of custom apparel, DTF printing stands out as a game-changing technology that makes it possible for producers and designers to create bespoke apparel with exceptional detail and top quality. Direct-to-film (DTF) printing has actually transformed the custom fashion industry by supplying versatility in design, vivid shade reproduction, and resilience. This innovative technique permits detailed layouts to be moved onto a vast variety of fabrics without compromising look at here the stability of the material.
One substantial application of DTF printing remains in developing custom-made t-shirts, hoodies, and sports apparel. The capacity to print complicated graphics with great details and slopes makes it suitable for customized apparel, such as team uniforms and marketing merchandise. In addition, DTF printing is especially useful for limited-run orders and one-off items, supplying a efficient and cost-efficient remedy compared to standard screen printing approaches.
Additionally, DTF printing has opened up new methods for designer to trying out distinct patterns and structures, enabling the creation of cutting-edge, avant-garde collections. This technology additionally supports small companies and independent musicians by lowering the obstacles to entry in the personalized clothing market. Inevitably, DTF printing is improving the landscape of personalized clothing, combining creative expression with technical innovation.
Versatility Across Different Products
Structure on the improvements in customized apparel, DTF printing's flexibility across different products additionally boosts its allure. Unlike traditional printing methods, DTF (Direct-to-Film) printing can be applied to a comprehensive description array of substrates, consisting of cotton, polyester, blends, natural leather, and even tough surfaces like wood and glass.
The ability to print on diverse materials opens many possibilities for organizations across different sectors. In the advertising products market, companies can personalize a broad range of items, from tote caps and bags to cups and phone instances, all with the same printing innovation. In the fashion business, DTF printing enables designers to trying out elaborate patterns and vivid colors on non-traditional materials, pressing the borders of creativity.
Moreover, DTF printing's compatibility with different products additionally converts to cost-efficiency and reduced waste, as suppliers can make use of the very same tools for multiple applications. This adaptability not only widens the extent of item offerings but also improves functional performance.
Future Leads of DTF Printing
As the market advances, the future leads of DTF printing are positioned to change numerous sectors with constant advancement and technical improvements. The surge popular for tailored garments and marketing goods is driving the need for much more effective, flexible, and economical printing methods. DTF printing, with its capacity to generate top notch, long lasting prints on a wide variety of materials, stands at the leading edge of this change.
Emerging patterns suggest that DTF printing will increasingly integrate with automation and AI technologies, enhancing manufacturing rate and lowering labor prices. Advanced software application services will better enhance design precision, shade matching, and print consistency, dealing with some of the existing restrictions. Additionally, green inks and recyclable transfer films are anticipated to acquire traction, straightening with worldwide sustainability goals.
As study and development initiatives continue to expand, the range of DTF printing will likely broaden, opening up new opportunities for innovative and commercial applications. In recap, the future of DTF printing is bright, appealing substantial improvements and broader market adoption.
Conclusion
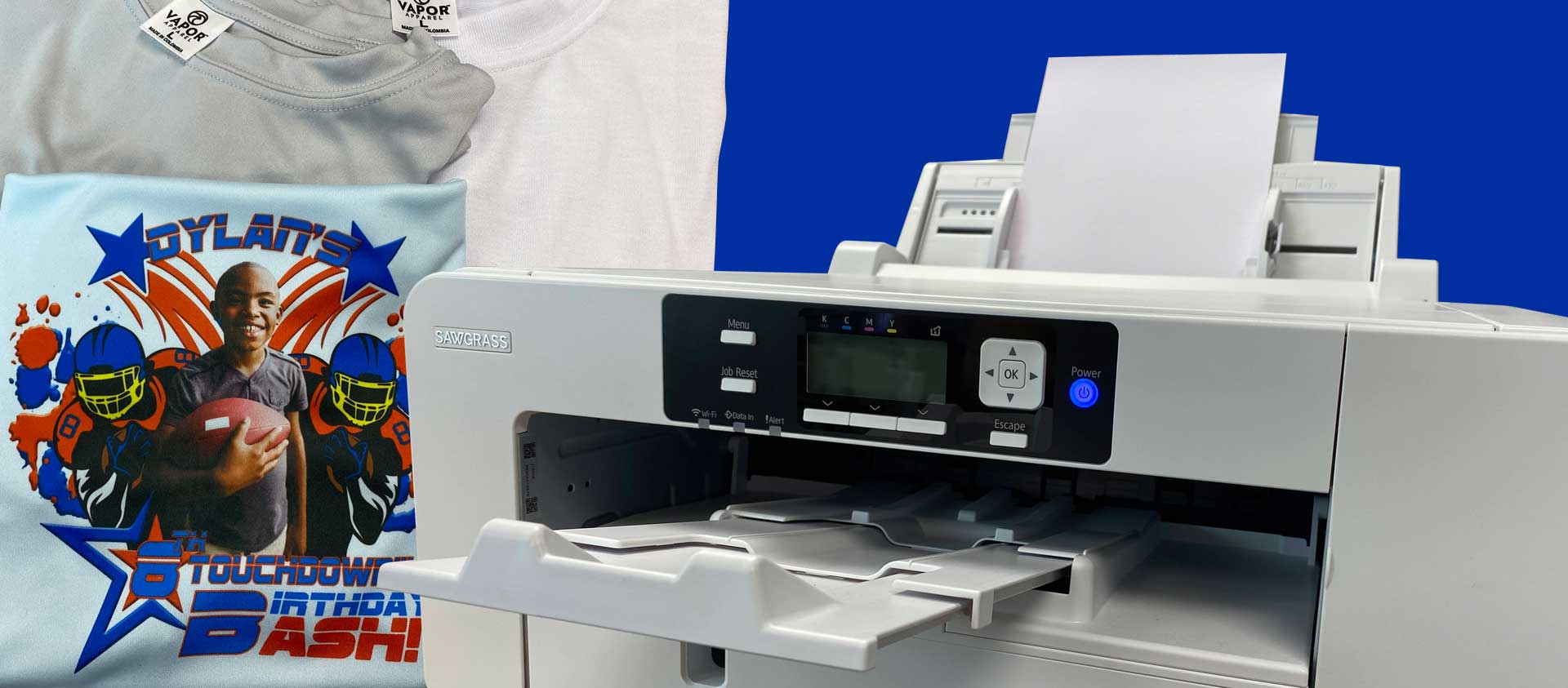
Comprehending DTF Printing Modern technology notes a significant improvement in the textile printing industry, specifically for its convenience and effectiveness. Direct-to-Film (DTF) printing is an advanced process that involves printing layouts onto unique transfer movies, which are after that moved onto textile utilizing warm and pressure. DTF printing is particularly useful for limited-run orders and one-off items, offering a cost-efficient and effective service compared to conventional screen printing methods.
Unlike typical printing techniques, DTF (Direct-to-Film) printing can be applied to a considerable variety of substrates, including cotton, polyester, blends, leather, and also difficult surfaces like wood and glass.DTF printing technology is revolutionizing the custom garments industry by offering reliable, affordable, and functional services for generating lively designs on different fabrics without pre-treatment.